Transforming propylene oxide to propylene glycol is an industrial process that holds significant importance in multiple sectors, from the production of pharmaceuticals to the development of resins and antifreeze agents. This intricate conversion process not only requires a high level of technical expertise but also an authoritative approach to ensure safety, efficiency, and sustainability in manufacturing.
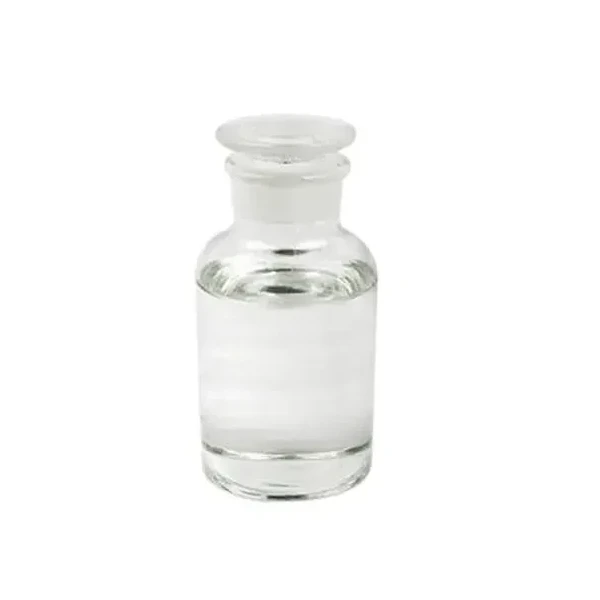
The journey from propylene oxide to propylene glycol centers on the principle of hydrolysis, where propylene oxide (a highly reactive and volatile epoxide) undergoes a reaction with water. In this conversion, understanding the chemistry is paramount. The presence of a catalyst such as a strong acid or base facilitates the reaction’s speed and efficiency, reducing energy consumption and operational costs. This is where industrial expertise comes into play, as selecting the appropriate catalyst can significantly influence the quality and purity of the propylene glycol produced.
With a background deeply ingrained in chemical engineering, I have extensively explored the nuances of this conversion process. A key factor in ensuring the production of high-quality propylene glycol involves maintaining optimal reaction conditions, including temperature, pressure, and catalyst concentration. For instance, controlling the temperature is critical; too high a temperature can lead to unwanted byproducts, while too low a temperature might slow down the reaction rate, impacting productivity.
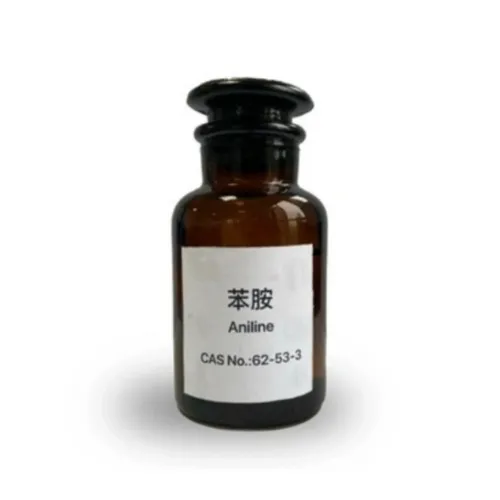
In terms of equipment and technology, this process benefits from modern advancements such as continuous reactors, which allow for better control and consistency in product quality. The use of advanced monitoring and automation systems provides real-time adjustments, ensuring that the reaction remains within optimal parameters, thus yielding a more consistent and reliable product.
propylene oxide to propylene glycol
Trustworthiness in this process comes from rigorous compliance with industry regulations and standards. Manufacturers must ensure that every step of the production complies with safety norms and environmental guidelines. This is not merely a legal obligation but a commitment to quality and responsibility towards consumers and the environment. Implementing quality assurance processes such as regular testing and thorough documentation guarantees that the propylene glycol produced meets the highest standards for purity and performance.
Moreover, sustainability is a growing concern in chemical manufacturing, and the conversion of propylene oxide to propylene glycol is no exception. By integrating sustainable practices such as recycling energy and reducing waste, manufacturers can not only cut costs but also minimize their environmental footprint. The adoption of green chemistry principles can further enhance the environmental performance of this process, making it more sustainable and responsible.
In conclusion, the conversion of propylene oxide to propylene glycol is a multifaceted process requiring a blend of scientific expertise, engineering skill, and a commitment to quality and sustainability. By focusing on these aspects, manufacturers can not only optimize their production processes but also ensure the delivery of high-quality products that meet the needs and expectations of a diverse range of industries. As the demand for propylene glycol continues to grow, staying at the forefront of technology and best practices will be crucial in maintaining a competitive edge in the market.